Summary
Owns the process knowledge of the product(s) assigned throughout the commercial lifecycle, maintains the oversight on process capability, through data trending and statistical analysis of critical variables, ensuring process(es) are robust, in continued state of validation and continuously improving.
About the Role
Major accountabilities:
Stewardship
- Maintain the oversight and knowledge for entire manufacturing process performed on site and throughout the entire commercial lifecycle
- Create and maintain a product specific Quality Risk Analysis (QRAs).
- Ensure creation of Master Batch Record.
- Lead / support root cause investigation of process failures, initiate and lead product improvement projects, involving cross-functional teams.
- Ensure inspection readiness for all process related aspects of assigned products.
- Track and evaluate product performance, trending, detect issues, implementation of CAPAs.
- Monitor all critical variables and key variables as appropriate using statistical analysis and conducting regular product specific data trending.
- Present product performance and status of product improvement projects in site Manufacturing Robustness Review Board (MRRB).
Validation
- Define and implement validation strategy (process, cleaning, ongoing verification) and defend to authorities.
- Overall responsibility for establishment, prioritization, execution and tracking of Validation Master Plan for process, cleaning, packaging validation and ongoing process verification (OPV), ongoing cleaning verification.
- Ensure that all manufacturing and cleaning processes are validated, overview on state of validation at site is maintained.
- Establish and monitor validation KPIs.
- Maintain all validation activities in an inspection ready status. Product is maintained in constant state of validation.
- Author complex validation protocols.
- Establish local procedures & templates for respective validation documentation.
- Ensure that all Site validation activities are performed and are in line with the current Novartis requirements and cGMP, handling any deviations associated to these activities including oversight of pre-validation and validation resulting from technical changes.
- Provide technical expertise (and may facilitate) pre-validation risk assessments using risk management tools.
- Be a senior advisor in case of difficult validation challenges at Site.
- Host validation council.
- Support Site MS&T Head in ensuring that responsible departments execute and maintain the VMP activities.
- Partner with Engineering, IT, QC, AS&T to define the interfaces to equipment qualification / utilities qualification, system qualification, analytical method validation.
- Ensure that the ongoing verification report (OPV) is established on time in alignment with the APQR.
- Ensure inspection readiness for all process related aspects of assigned products.
Performance Qualification
- Prepare Qualification documents of equipment with leverage to Global standard Qualification approach/practice.
- Engage cross functions including 3rd party to ensure that all PQ activities are performed and are in line with the current Novartis requirements and cGMP, handling any deviations associated
- Ensure PQ activities and Documents along within project schedule and budget.
- Facilitate execution of integrated line PQ, provide insight to finalize process design.
Launch & Transfer
- Participate in transfers and launches, Provide technical expertise for pre-validation / validation strategy.
- Create documents requirement in MPT
- Contribute to providing experimental data obtained during the validation activities, which will be used to prepare the related registration documentation.
Manufacturing Excellence
- Provide SME expertise to perform process characterization of pharmaceutical processes to increase robustness and sustainability.
Training
- Own the Training Curriculum for own Profile and direct reports.
Novartis Manufacturing Manual
- Support implementation of Novartis Manufacturing Manual principle 3.
- Represent site in validation network.
Key performance indicators:
- Validation Master Plan (VMP) completed and up to date.
- Product maintained in a constant state of validation.
- Transfers/launches implemented on schedule and on target without validation related issues. Deliver validation data that meet the target schedule and quality to support the required registration documentation.
- Validation approach meets Novartis QM requirements, health authority and industry standards.
- OoS, OoE, Deviation, CAPA, compliant, recall – process-related.
- Completeness of Regulatory CMC dossier.
- All related SOPs are updated on time.
- Success rate of Health Authorities’ inspections.
Minimum Requirements:
Work Experience:
- 8-year experience in manufacturing / manufacturing science and technology / technical development / quality of aseptic process.
- Thorough understanding of manufacturing processes and related process equipment.
- Strong working knowledge of applied statistics, quality systems and regulatory requirements across multiple health authorities.
- 5-year experience in executing process validation, having led and managed validation projects, process support, e.g. Process Expert role on the shop floor of pharmaceutical manufacturing and/or QA/QC.
- Expert in reviewing and writing technical reports.
- Proven project management experience in a cross-functional environment (e.g. multi-site, technical development, other functions).
- Fundamental understanding of standard pharmaceutical analytical testing.
- Proven process understanding (Pharma, GMP, Regulatory aspects).
- Sound experience of data handling and applied statistics is a must.
Skills:
- Knowledge Of Gmp.
- Manufacturing Process & Technologies.
- Process Validation & Process Control.
- Control Strategy and Process Performance Monitoring
- Risk Management.
- Applied Statistics.
- General HSE Knowledge .
Languages :
- Fluent in English and proficient in country language.
Why Novartis: Helping people with disease and their families takes more than innovative science. It takes a community of smart, passionate people like you. Collaborating, supporting and inspiring each other. Combining to achieve breakthroughs that change patients’ lives. Ready to create a brighter future together? https://www.novartis.com/about/strategy/people-and-culture
Join our Novartis Network: Not the right Novartis role for you? Sign up to our talent community to stay connected and learn about suitable career opportunities as soon as they come up: https://talentnetwork.novartis.com/network
Benefits and Rewards: Read our handbook to learn about all the ways we’ll help you thrive personally and professionally: https://www.novartis.com/careers/benefits-rewards
Accessibility and accommodation
Novartis is committed to working with and providing reasonable accommodation to individuals with disabilities. If, because of a medical condition or disability, you need a reasonable accommodation for any part of the recruitment process, or in order to perform the essential functions of a position, please send an e-mail to [email protected] and let us know the nature of your request and your contact information. Please include the job requisition number in your message.
Novartis is committed to building an outstanding, inclusive work environment and diverse teams' representative of the patients and communities we serve.
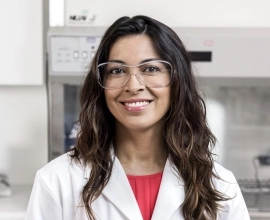